ANSYS FLUIDS
Computational Fluid Dynamics (CFD) Simulation Software
With engineering knowledge, we can govern the flow to our advantages. Computational Fluid Dynamics (CFD) provides insights for designing and validating our equipment.
R1 2024
Fast, Accurate CFD
Ansys CFD products give you the possibility to make incredible progress through innovation as pressures to optimize products ratchet up and margins for error narrow quickly. Comprised of the industry’s most accurate and trusted solvers, you will have confidence in your results. Whether you want to maximize the efficiency of an internal combustion engine or perform an in-flight icing simulation, Ansys has the tool for you. Maximize your time and increase productivity with modern, user-friendly Ansys CFD products.
Fluids Products
Ansys Fluent
CFD software distinguished by its sophisticated physics modeling and acclaimed for its industry-leading precision.
- Modern user-friendly interface.
- Single window workflow pre to post-processing.
- Streamlined meshing and physics workflows.
- Advanced physics modeling.
- Efficient meshing and solver HPC scaling.

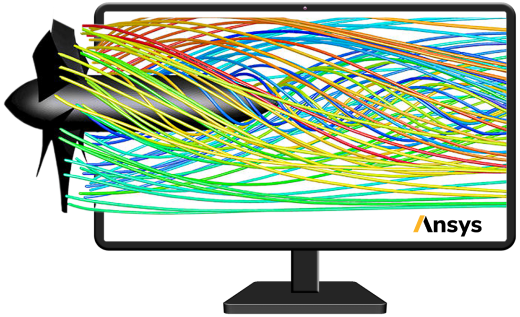
Ansys CFX
High performance CFD software recognized for outstanding accuracy, robustness and speed with turbomachinery applications.
- Streamlined turbo setups.
- Blade design tool integration.
- Multi-stage CFD modeling.
- Transient blade row methods.
- Harmonic balance methods.
Ansys Forte
Exceptionally reliable CFD software for internal combustion engines and positive displacement compressor design.
- Automatic mesh generation.
- Adaptive mesh refinement.
- Validated kinetics models.
- Automated workflows.
- Fast chemistry solver.
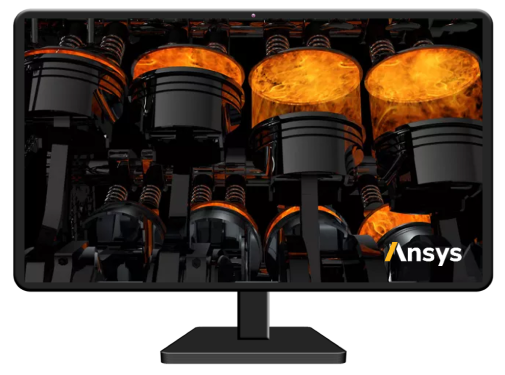
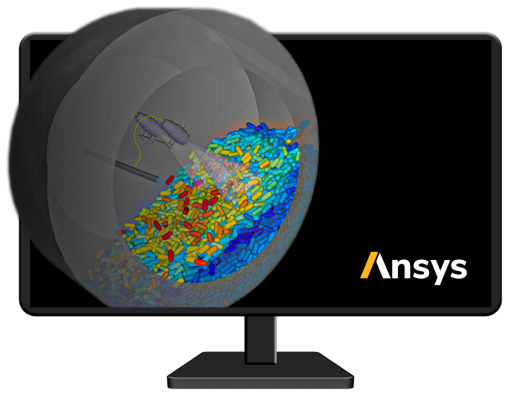
Ansys Rocky
Stands out for its ability to accurately model real particle shapes, including solid objects, 2D shells, and both rigid and flexible fibers. The simulations conducted with Rocky are both swift and precise.
- Multi-GPU solver.
- Scalable, efficient, large particle counts.
- Realistic particle shapes including fibers.
- Wear modeling, particle breakage, cohesion.